By Edward Taylor, Alexandria Sage
5 Min Read
LANDSHUT, Germany (Reuters) - German auto maker BMW Group is limiting its use of costly carbon fiber and turning to cheaper lightweight materials such as aluminum and steel for its biggest selling cars to keep profit margins high.
A BMW logo is seen on media day at the Paris auto show, in Paris, France, September 30, 2016. REUTERS/Benoit TessierLighter cars consume less fuel or if they are battery-powered can drive for longer on a full charge, vital attributes for manufacturers seeking to score points with consumers and regulators.
But there is a trade-off. Although carbon fiber is stiffer and lighter than aluminum, it is more expensive, and BMW faces tough choices on how to remain profitable as competitors close in with their own lightweight electric car offerings.
BMW is now combining carbon fiber with other lightweight materials to shave weight from cars without making them too expensive.
“The main equation is how much cost do I spend for a kilogram reduction in weight. It is not about one material it is about the combination of materials,” Oliver Zipse, BMW’s board member responsible for manufacturing, said at the opening of a new 20 million euro high-tech research facility specializing in lightweight materials.
The lighter you can make an electric car, the less you need a large battery to power it, saving costs. Batteries are the most expensive part of electric vehicles, which remain an unprofitable segment in the auto industry.
After launching two cars which made heavy use of carbon fiber including the i3 city car and the i8 hybrid in 2013, BMW’s new 5-series, presented earlier this month, does not use the material for major components.
Sales of BMW’s i3 electric car have failed to take off, analysts say, in part because of the extensive use of carbon fiber, which has made the vehicle expensive. It costs around 45,000 euros.
Competitors such as Tesla are planning to launch models for around $35,000, and have received up to 400,000 pre-orders for these more affordable vehicles.
BMW is now working on ways to further reduce the costs of incorporating carbon components into mass production and is making good progress, Zipse said.
Carbon fiber, which needs to be bonded and glued together rather than stamped or welded, costs around 16 euros per kilo, compared with less than a euro for a kilo of common steel, according to consultants at Frost & Sullivan.
The costs of carbon fiber are expected to come down as its use becomes more widespread in industries such as aircraft manufacturing, Boston Consulting Group said. If luxury cars use only 1 percent of carbon fiber, the market for automotive components could grow from about $250 million to around $3 billion in the next 10 years.
Several carmakers have entered technology cooperation deals with specialist companies to push advances in carbon manufacturing. BMW has a cooperation deal with SGL Carbon , General Motors with Teijin, and Audi with Voith [VOITH.UL] and Daimler with Japan’s Toray Industries.
BMW already makes some components for its new 7 series out of carbon. But this is only possible because it is a high margin model.
BMW is under pressure to raise its game as German rivals Daimler AG, parent company of Mercedes-Benz and Volkswagen AG VOWG_p.DE, which owns Audi, as well as Tesla Motors Inc in the United States have outlined aggressive plans to court affluent buyers with new electric cars.
BMW said last month it would expand its electric offerings with all-electric versions of the Mini and its BMW X3 compact sport utility vehicle in 2019 and 2020, respectively.
Zipse declined to comment on whether future BMW and Mini vehicles will make extensive use of composite materials. BMW Chief Executive Harald Krueger was more direct, effectively ruling it out for smaller low margin cars.
“The material is still too expensive and for smaller segments and smaller vehicles it can be not competitive,” Krueger said at an event in Los Angeles earlier this month.
Advances in battery technology have improved vehicle operating range by about 50 percent since 2013, taking some pressure off the need to use ultra expensive lightweight materials in manufacturing.
After investing between 1.5-2 billion euros to develop carbon-fibre based hybrid and electric cars, BMW is now working hard to develop “hybrid” methods, which combine carbon with other materials like steel and aluminum.
BMW’s past investment in carbon fiber will be a great help, said Jochen Kopp, who specializes in product and process planning for carbon fiber reinforced plastics.
The Munich-based carmaker now has a two year lead on rivals in terms of carbon fiber mass production know-how, he said.
“It takes time to learn how it behaves in manufacturing, how it reacts to being bonded to other materials. This has implications for tooling, purchasing and manufacturing. We understand the complete development chain,” Kopp said.
(This story has been refiled to fix garble in first paragraph)
Reporting by Edward Taylor; editing by Alexandra Hudson and Jason Neely
Our Standards: The Thomson Reuters Trust Principles.

The 15 Most Expensive BMWs Ever Built Elite Traveler

The BMW i15 Why It Is the Most Expensive Hybrid Sports Car In
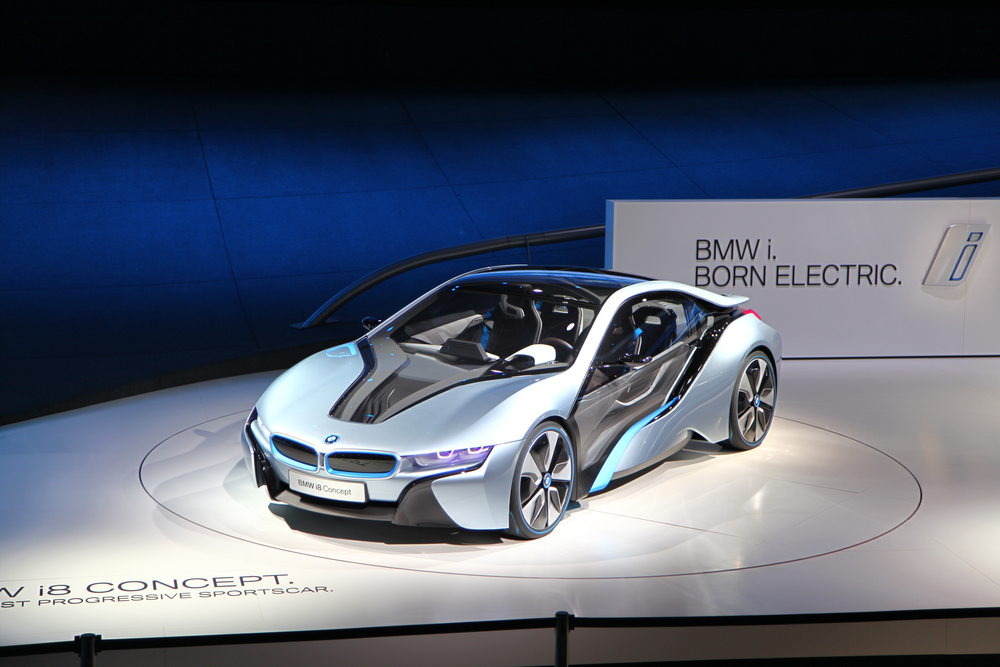
The BMW i15 Why It Is the Most Expensive Hybrid Sports Car In

15 of the Most Expensive Electric Cars Autobytel
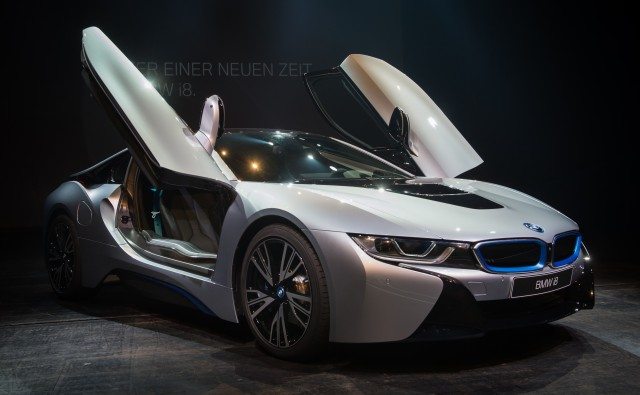
The 15 Most Expensive BMWs Ever Assembled

Most Expensive BMWs in the World Alux

BMW X15 To Become Most Expensive Model From The Brand Bmw Bmw x15
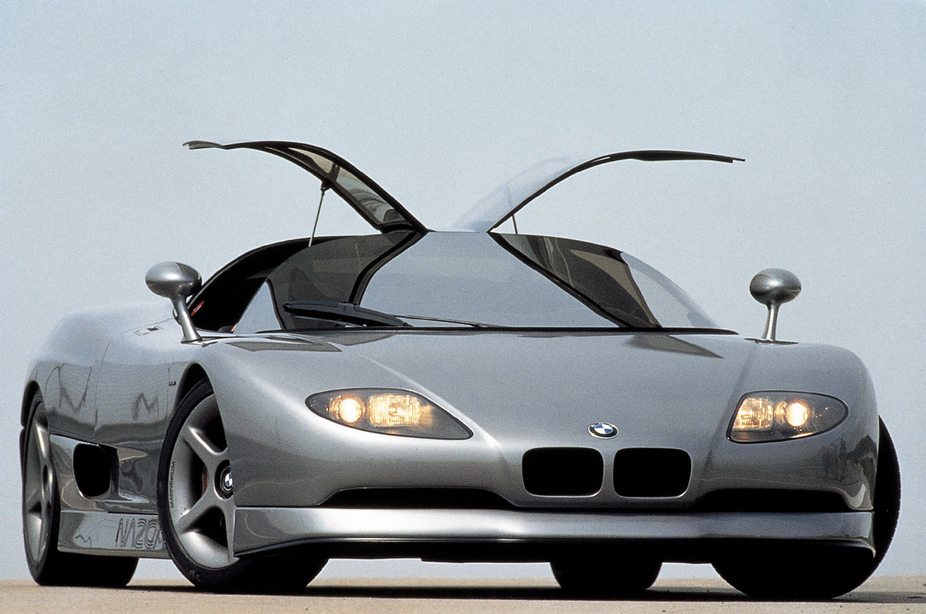
The 15 Most Expensive BMWs Ever Coast Motor Werk
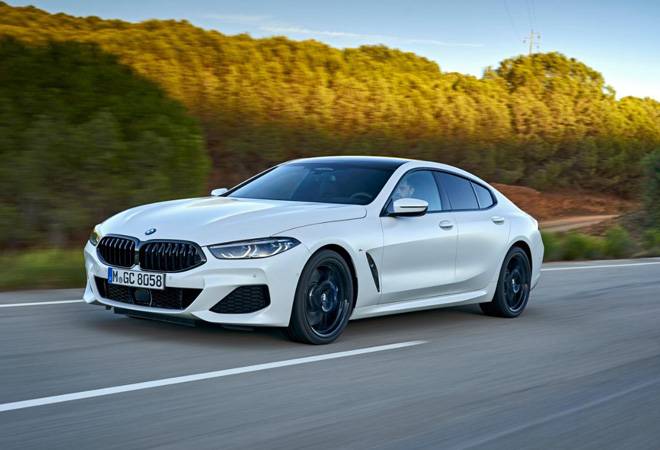
Super expensive BMW launched in India Luxury car M15 coupe costs
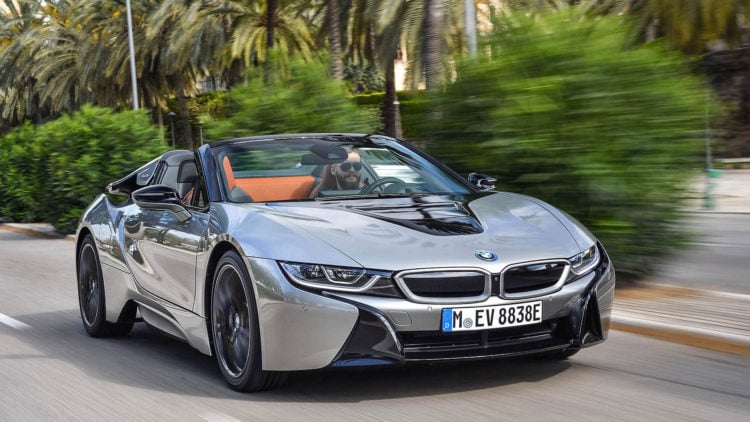
The 15 Most Expensive BMWs Ever Built

The 15 Most Expensive BMWs Ever Built
Why are BMW cars more expensive than Toyota cars Quora

What is the most expensive BMW UAE YallaMotor
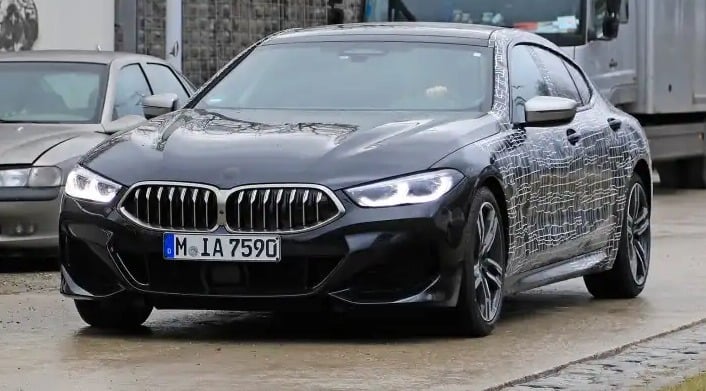
The 15 Most Expensive BMWs Ever Built

The 15 Most Expensive BMWs Ever Built